So why are we seeing abrasive damage occurring? At entry into marine engines of deep-sea and short sea vessels, the level of CAT fines is limited to 7mg/kg - 15mg/kg, which is great. However, fuel oil is not supplied at a maximum of 7mg/kg Al+Si.
ISO 8217: 2005 stated that CAT fines (Al+Si) were to be maximum of 80mg/kg, when in 2010 suggested that the level be reduced to 60mg/kg, with ISO 8217: 2017 further suggesting the same at 60mg/kg. Consequently, a considerable amount of processing is required prior to fuel oil entry at the engine of no more than 15mg/kg of Al+Si abrasive.
Whilst there is a need to reduce the potentially present 60mg/kg Al+Si down to engine manufacturers’ allowable limit of 7mg/kg – 15mg/kg, an effective fuel oil processing system and fuel oil management plan is essential on-board any vessel.
It is often easy to install and manage the fuel oil treatment system on-board deep sea and short sea vessels; however, small commercial craft are unable to accommodate the extent of the deep sea and short sea fuel oil processing equipment due to their size.
Small commercial craft are unable to segregate fuel oil until fuel oil analysis reports have been received, often not possessing purifiers or filtration systems other than that supplied with the engines, directly due to the size of the vessels as suggested in the table below.
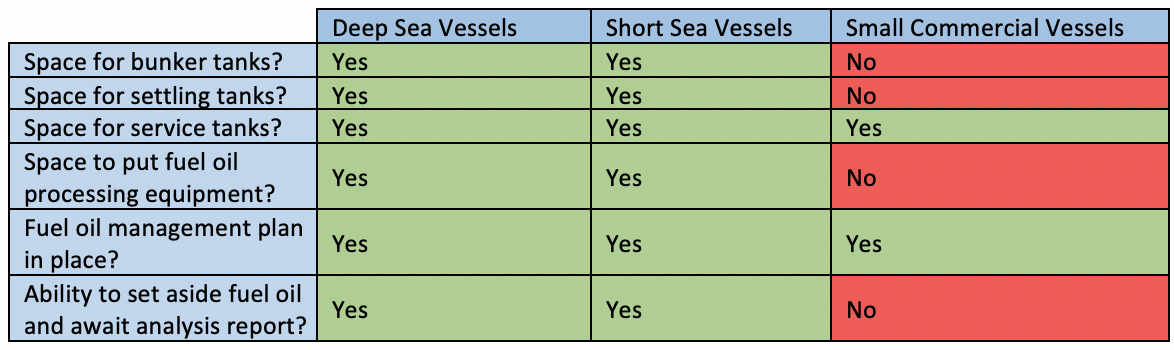
Whilst the deep sea and short sea vessels have fuel oil treatment systems and managements plans to effectively reduce the Al+Si to 15mg/kg or lower, they are often met with poor fuel oil quality in the first instance.
Small commercial craft are at a further disadvantage, with their on-board engines producing considerably more power now than they ever did ten years ago for the same size and weight, and as a result poor fuel oil quality cannot be tolerated by such equipment.
Consequently, some engine manufacturers have specified cleanliness in lieu of fuel oil tanks/processing equipment - ISO 4406 cleanliness code (18/16/13).
ISO 4406: Code A/B/C
- first number (A) denotes particle count of size ≥4μm per 1.0ml
- second number (B) denotes particle count of size ≥6μm per 1.0ml
- third number (13) denotes particle count of size ≥14μm per 1.0ml
- first number (18) denotes that there are more than 1,300 up to and including 2,500 particles of size ≥ 4μm per 1.0ml
- second number (16) denotes that there are more than 320 up to and including 640 particles of size ≥6μm per 1.0ml
- third number (13) denotes that there are more than 40 up to and including 80 particles of size ≥14μm per 1.0ml
- Know your engine manufacturer’s requirements for fuel quality and adhere to it.
- Know your vessel’s ability to process fuel oil to the engine manufacturers’ fuel oil requirements.
- Train personnel to understand the risks and operate fuel processing equipment effectively and monitor effectiveness routinely.
- Monitor fuel quality throughout fuel management process and in particular prior to entry into engine.
- State very carefully what specification of fuel is required, including year of specification ISO8217: 2012 / 2017 or ISO 4406: (18/16/13).
- Correctly sample fuel being bunkered and retain samples as per MARPOL.
- Correctly label samples and send for analysis ASAP.
- Isolate FO being bunkered where possible and obtain analysis prior to burning.
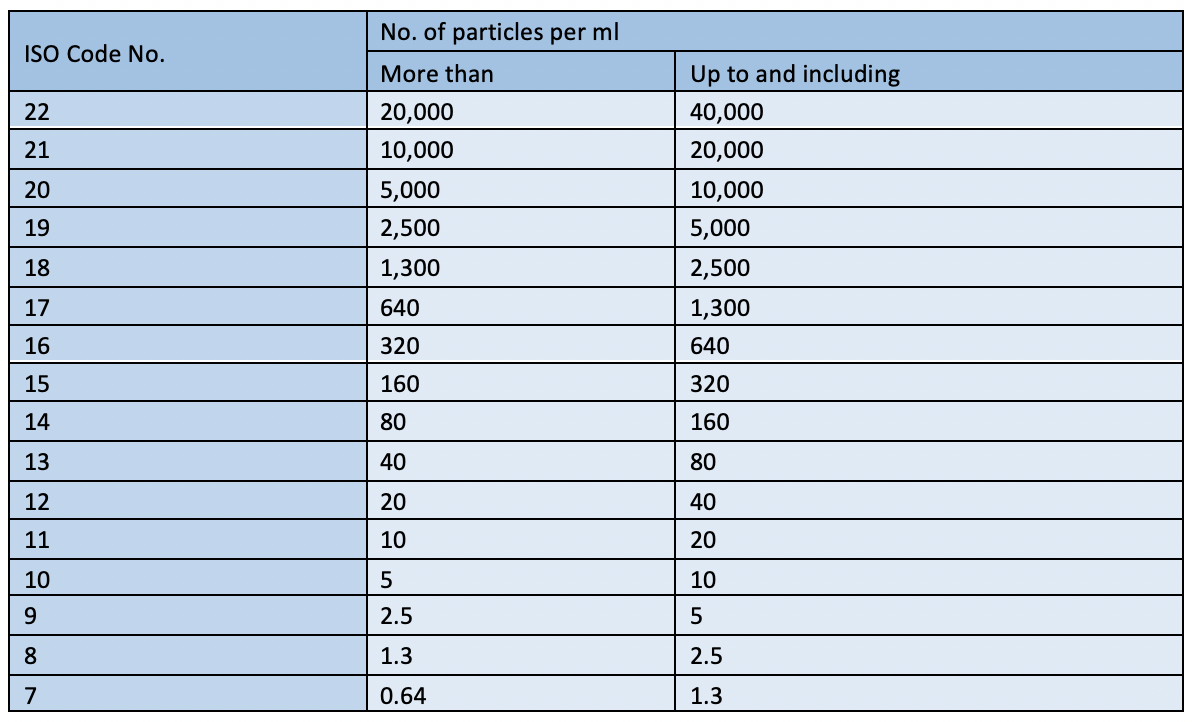
So are we out of danger? No, as there is a small amount of particulate which may or may not be abrasive, so filters to protect against 4µm and below are necessary on-board these vessels.
So it’s great news that MGO fuel oil can be supplied at ISO 4406: (18/16/13); however, we’re still seeing issues of poor quality MGO with excessive abrasive matter and whilst the issue is not wholly attributable to fuel oil suppliers, vessel owners have not been fully aware of ISO 4406: (18/16/13) when making charter party agreements. Meanwhile H&M/P&I Insurers are expected to pick up the tab.
Summary
- Know your engine manufacturer’s requirements for fuel quality and adhere to it.
- Know your vessel’s ability to process fuel oil to the engine manufacturers’ fuel oil requirements.
- Train personnel to understand the risks and operate fuel processing equipment effectively and monitor effectiveness routinely.
- Monitor fuel quality throughout fuel management process and in particular prior to entry into engine.
- State very carefully what specification of fuel is required, including year of specification ISO8217: 2012 / 2017 or ISO 4406: (18/16/13).
- Correctly sample fuel being bunkered and retain samples as per MARPOL.
- Correctly label samples and send for analysis ASAP.
- Isolate FO being bunkered where possible and obtain analysis prior to burning.
When purchasing
Remember 7mg/kg – 15mg/kg of Al+Si abrasive on entry into low and medium-speed engines, with ISO 4406: (18/16/13) on high-speed engines.